There is no warp beam on the
back of the West African strip looms—only what is called
by Eric Broudy (The Book of Looms) a "diverting
bar". The warp travels over
the diverting bar and stretches its full length across the
compound’s courtyard. The warp is then tied to a weight or
stone—this weight both anchors the warp and maintains even
tension. This weight is called a "drag Stone". As
the weavers weave and pull the warp forward the stone is
dragged along the dirt towards the weaver. In many villages
you can see the path the stone makes as it is dragged closer
and closer to the loom.
The warp is prepared either
in the courtyard of the compound, out in the streets of the
village or any place where there is enough space. If space
is a problem—as in some towns in Mali, the professional
Warp Preparer will wind the warp around his house. However,
when there is enough space poles three feet in height are
used. They are hammered in the dirt and spread evenly apart.
A forked tree branch is sometimes used to maintain the
cross. For an Ashante man’s cloth (or toga) which is
usually 24 strips wide and approximately 3 yards long, the
warp has to be 32 yards long. The warp poles are arranged in
any manner that is convenient to obtain this warp length.
The Warp Preparer—which is an occupation akin to that of
the weaver—knows from memory the required length and color
rotation for a specified pattern.
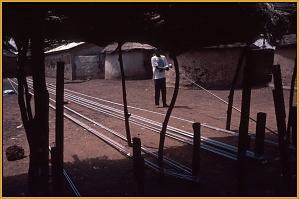
After the warp is prepared,
it is wrapped onto large bobbins, which are then placed on
the tines of a bobbin carrier. This bobbin carrier is called
in Ashante "menokomenam", which means
"I walk alone". From the bobbin carrier the warp
is transferred to the shuttles.
Treadles are also simple in
construction. Twine is tied to the harnesses—at the end of
the twine are knobs which are made from a calabash gourd.
These knobs are placed between the toes of the weaver. As
the weaver’s feet move up and down so do the harnesses. In
Mali a knot is made at the end of the twine and this knot is
placed between the weaver’s toes. In both instances the
function is the same—the weaver’s feet become the
treadles.
Weaving is done outside and
is a social activity. Small sheds or fronded roofs are built
to protect the weavers from the heat of the sun. Shade from
trees also can protect the weaver from the mid-day heat. As
I wandered through a village I would see weavers working
together with their long warps stretching far into the
compound. Up to three yards of woven fabric is made during
one day’s weaving. At the end of the day the weaver
dismantles his loom and takes it inside the house for the
evening.
A weaver I met in Timbuktu
(Mali) demonstrated for me the ease of dismantling a loom.
He was weaving in a guildhall in the city of Timbuktu. I
arranged to meet with him at the end of the day—he wanted
me to meet and have dinner with his family. He took his
warp, the reed and woven fabric, wrapped them into a ball
and placed them into a bag. He then untied and collapsed his
loom, bound the loom pieces together, put the loom on his
head and shoulders and carried it home.
|